Accuracy, speed, lowered costs and durability are the foundations of success for businesses across industries.
These are the attributes your customers seek from your product. When your business is looking to bring a high-quality product into the market and achieve a competitive edge, the precision of your products’ components is paramount.
Plastic injection moulding is an optimal solution that offers precision, accuracy, durability and cost savings for your business with the ability to fabricate any plastic component of varying complexity.
The multiple benefits offered by the process is the reason why a growing number of businesses are using injection moulding for manufacturing components and products. According to recent research, by 2025, the global injection moulding market revenue is slated to reach $500 billion. There is a growing demand for injection moulding in regions across the world, including South Africa, with a 4 per cent annual increase in demand.
There are many reasons why injection moulding is emerging as one of the most popular technologies.
The steps in the injection moulding process
The first step is the product design, which is completed by an engineer or industrial designer. Based on the design, the mould is then prepared by a toolmaker using Sophisticated CNC machining process to cut aluminium or steel.
The process involved in injection moulding involves closure of the mould, injection of plastic into the mould, melting and cooling of plastic, ejection of the finished part, and finally, packaging of the product.
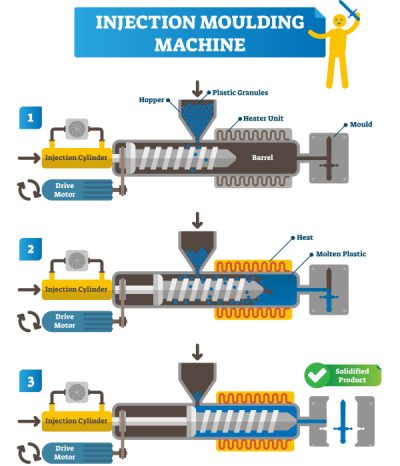
Clamping or closure
The injection moulding process begins with the closing of the mould’s halves. A clamping unit closes the mould halves which are then presented to the barrel of the injection moulding machine. One half of the mould can move to and from the fixed half. Once the clamps have pushed together the two halves and the clamping pressure is reached, the moulding material can be injected.
Injection
Plastic pellets are introduced into the injection moulding machine with the help of a hopper. These pellets gravitate towards the mould near the injection unit. The heat and pressure that is applied the barrel ultimately melt the pellets.
A hopper feeds plastic pellets into the moulding machine. The plastic pellets melt due to the pressure and the heat around the barrel, and the melted plastic is then injected within the mould.
As the melted plastic enters, it displaces air, which escapes through the vents located along the splitline of the part and/or ejection pins across the part face. The design of the gate, runner and vents are crucial to ensure that the mould gets properly filled.
When the mould is filled between 95 to 99 per cent, the injection timing is complete. Injection time is also estimated with other factors, including shot volume (the volume of material) power and injection pressure.
Cooling
After the mould is precisely filled, the cooling process begins where the part is cooled for the exact duration required for the material to harden. Cooling time depends on the resin type as well as the part’s thicknessEvery mould is designed optimally with internal heating or cooling lines with water being cycled through in order to maintain a constant temperature.
Ejection
The mould then opens, and the ejector pins are moved forward by the main ejector rod. The moulded part drops and is collected in a bin or drop shoot that is located beneath the mould. If the part requires sensitive handling or the speed of production is unsafe for human access, the use of robotic arms is typically used during the de-moulding process
Removing/recycling runner and packaging
The process continues with the separation of usable parts from the runner, which is the pathway the plastic uses to fill up the mould cavity.
The runners may be ground and recycled in order to minimize environmental impact and to reduce costs. In higher volume products, the use of a hot-runner system can be implemented to eliminate the need for recycling cold runners.
The usable parts taken from the runner are counted, quality checked, weighed and packaged for shipping or for assembly.
Benefits of injection moulding
Injection moulding is a highly versatile method of manufacturing products and parts. Businesses across industries prefer injection moulding to manufacture parts given its multiple advantages as compared to other plastic moulding processes. Not only is the injection moulding process more reliable and simpler, but the method is also extremely efficient.
The top benefits of injection moulding include:
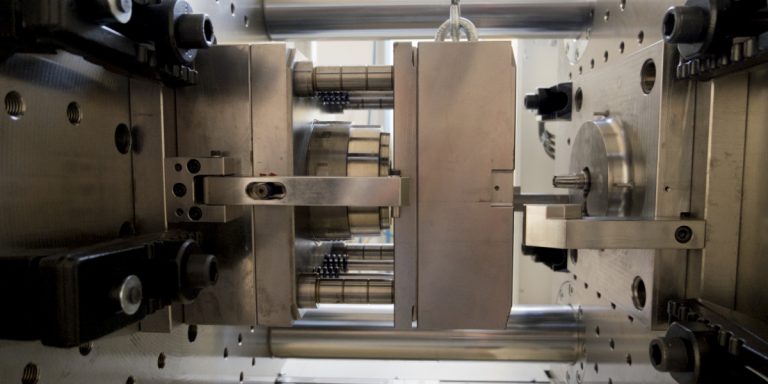
Capacity to produce highly detailed and complex parts
Leading injection moulding manufacturers adopt a scientific approach to moulding and tool design. This helps optimize the process and ensures the production of detailed and extremely complex plastic parts.
A streamlined, efficient process
A sophisticated injection moulding manufacturer has a highly experienced team of designers and engineers apart from established quality control processes. This ensures that both the design and manufacturing processes are optimized and streamlined to enhance efficiency.
After the designing of injection moulds as per customer specifications and pre-programming of the machine, the process of moulding is very quick in comparison to other plastic moulding processes.
Injection moulding is also fast. Although the speed generally depends on the mould’s complexity and part size, the time taken for each cycle of production is between fifteen to Sixty seconds Depending on the tool design – Multi cavity tools can allow for parts to be produced in a fraction of a second.
Cost-effectiveness
With reduced time and heightened efficiency, more parts can be manufactured using a single mould. Efficiency goes hand in hand with cost optimization. Given the high rate of production output, plastic injection moulding reduces the cost of manufacturing.
Leading custom moulding facilities use an automated process with robotics that reduces overheads and costs of manufacturing significantly. This also enables 24-hour operations which ensures a quicker delivery and zero wastage.
Enhanced strength and durability of product
Different material grades, material fillers and additives allow for a wide range of applications in products – From flexibile to rigid materials or materials with high working temperatures, chemical resistances and or semiconductivity.
Injection moulding meets the key requirements of product durability and strength in a diverse range of industries from telecommunications to automotive, and furniture to hardware
Suitable for a wide range of plastics
A key advantage of plastic injection moulding process for manufacturing components relates to its ability to simultaneously mould various types of plastics. This is done using co-injection moulding that helps mitigate concerns with respect to any specific type of plastic.
In Conclusion
Injection moulding is ideally suited to produce high volumes of components. The parts manufactured in this process require minimal to no work in the post-production phase. This is due to the fact that parts produced in the method come very close to having a finished appearance when they are removed from the moulds.
With any generated scrap plastic being reused, injection moulding is an eco-friendly process that minimises wastage and lowers cost. These advantages eventually translate into a healthy bottom line for businesses.
Find out how PIMMS Manufacturing can help you with your next project.
Get your FREE
Ideas to Reality Product Process Checklist
Download our complete checklist to make sure you are covering all the steps it takes to create a product that will help you succeed in the market place